- Animal Feed Machine
- Animal Feed Production Line
- Fish Feed and Pet Food Machine
- Fish Feed and Pet Food Production Line
- Soybean Meal Machine
- Feather Meal Machine
- Biomass Wood Pellet Machine
- Biomass Briquette Machine
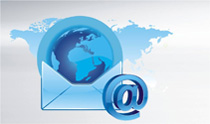
Email: carla@hnyearmega.com
Tel: +86 15093305912
Skype: zzhrsdcarlar
WhatsApp & WeChat: +86 15093305912
NEWS




Extrusion Technology and Feed Production Process Control
1. Extrusion Process and Main Kinds Applied in Feed Production
Its main equipment is “screw extruder”. The main kinds are fish feed extruder, soybean/corn extruder and feather extruder. Fish feed extruder is the common machine in fish feed pellet production, which includes single screw extruder and twin screw extruder.
The material is fed into the extruder and moves in the form of an axial flow under the screw power. At the same time, due to the mechanical friction between the screw and the material, the material and the barrel, and the material particles, the material is strongly squeezed, stirred, and sheared. As a result, the material is further refined and homogenized. With the gradual increase of pressure, the temperature rises accordingly. Under the condition of high temperature, high pressure and high shear, the physical properties of the material have changed as follows:
● From powder to paste.
● Gelatinization of starch.
● Protein denaturation.
● Partial degradation and refinement of fiber.
● Pathogenic bacteria were killed.
● Health indicators are improved.
● Toxic components were inactivated.
When the paste material is extruded from the die hole, under the influence of strong pressure difference, the material is expanded, dehydrated and cooled. The final product is of loose and porous structure, crisp, good palatability and flavor.
2. Extrusion process and characteristics of extruded products
2.1 Biochemical Process
The process of hydrothermal treatment is accompanied by the biochemical change process of the material. Some materials, such as oilseeds and their cakes, contain a variety of anti-nutrient and anti-feeding ingredients. Under certain moisture and certain temperature conditions, these active substances gradually lose their activity, weakening the destruction of digestive enzymes inside the digestive system of animals, which improves absorption rate and reduces excretion. This not only improves the nutrition value of feed, but also reduces waste and environmental pollution. From the view of the biochemical process, the extruder is a “biochemical reactor.”
2.2 High-temperature and short-term germicidal detoxification process
The highest temperature in the puffing process can reach(130-160) °C, while the material in the high temperature segment is very short, about 5-10 seconds. High temperature can not only kill pathogens and health indications, but also can inactive a variety of harmful factors and enzymes, improving the feed quality.
2.3 Better chemical stability and longer quality guarantee period
High temperature cause various microorganisms and parasitic ovum to be killed and various enzymes( such ad oxidase, lipase, etc.) are inactivated. That exclude a wide range of factors which contribute to deterioration of the material.
2.4 Wide range of process adaptability
Extrusion process can not only improve the feeding quality of a variety of common feed materials, but also can process a large number of unconventional materials into high-quality feed materials, which include wild plants, agricultural by-product, slaughter waste and of livestock and poultry, etc. Extruder machine can produce a variety of different specifications and quality of livestock and poultry materials, aquatic feed, pets feed, etc. At the same time, extrusion process is also the most effective techniques for the detoxification, preservation and processing of grain cakes and deep processing of grain.
2.5 High grade product features
● Uniform and denseAfter mixing, the raw materials is fed into the extrusion process. Each component is fully mixed, and melted into a uniform stream and then being extruded, puffed, cut and shaped. The pellet is loose, porous and density controllable. This characteristic of the expanded product can best meet the requirements of the aquatic product. The final products can be made into a sinking material or a floating material and the holding time of the material can also be adjusted by changing its density.
● Palatability and flavor
Extrusion products are loose and crunchy after being cooled, composite products produced by various components, and Maillard reaction due to high temperature, all these factors constitute the better palatablility over the original mixture and have a special flavor. These characteristics induce animal feed to intake, thus increasing feed intake and feed effectiveness. This is completely different from the addition of phagostimulant to the mixture, which often has negative effects.
2.6 It can produce special feed with different shape
According to he user’s requirements, changing the model design can produce different shapes of large particles, large blocks or bar-like materials, such as prawn feed, pet feed, rare animal feed, etc. This is what the ring die pellet machine can’t do.
2.7 Higher digestion rate
For those suckling pigs whose digestive system is not well developed, the starch in the weaning material requires the gelatinization degree of more than 90%. And the aquatic animals also requires the gelatinization degree of the feed should also be higher because their absorption capacity of the original degree is poor. Extruder machine can realize it well.
Therefore, it is better to use extruder than ring die pellet machine to produce aquatic products because due to the temperature restriction, the gelatinization degree of starch processed by ring die pellet machine can not be high, which is generally no more than 50%.
Gelatinization not only improves digestibility, but also improves granulation and shaping because dextrins are good binders. The gelatinized starch molecules crosslink each other to form a network-like spatial structure, lose some moisture after being instantaneously expanded, and become a skeleton of the expanded product after cooling, so that the product maintains a certain shape.